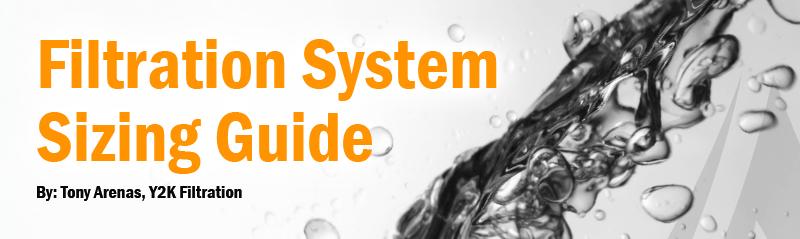
There is an insurmountable amount of information available about best practice oil handling, guides to a good reliability program and the importance of filtering your hydraulic and lubricating oils; but not much focus is put on how to properly apply a system based on various applications and conditions, information about what to consider when choosing a filtration system and how to verify that it meets the needs of the equipment or machine it will be applied to. This guide serves as a simple reference to help you in your next Filtration System purchase and implementation.
THE BENEFITS OF IMPROVING OIL CLEANLINESS WILL MEAN THE FOLLOWING:
- Increased Equipment Lifetime
- Longer Oil Service Life
- Reduced Lubricant Consumption
- Decreased Environmental Impact
“A few ISO code drops can increase machine reliability and life cycle by up to 5 times.”
Asking the Right Questions
There are some basic questions that come up when deciding which filtration system to purchase that are so simple they are often overlooked or omitted when specifying a filtration system. The inability to decide which system is going to work for you can really put a halt to any reliability program. With so many options and solutions it can become difficult and convoluted, so a price point is often reverted to with the idea if it doesn’t work out, well I don’t have that much invested in it. This is exactly the recipe for failure. With a change in the thought process, winning attitude for success and a few questions to consider, you can clearly see that a good filtration system applied properly can create a lot less pain, substantial return on investment, increased productivity and a healthier longer lasting system. Maintaining at a lower cost prior to system degradation, rather than cleaning an already contaminated system will allow for a substantial costs savings. So, let’s bring it down to the basics and go through the process of answering the questions that are going to help you in choosing the right system for your application.
“A contaminated system can cost as much as 10X more to clean than a maintained system”
Question #1: What is the Application?
There are so many applications in Industrial, Mining, Off-Road, Power Generation and the list goes on, so it’s important to know your individual system requirements to make informational based decisions that yield great returns. The reason application comes up as one of the first questions in sizing and applying a filtration system is it is very important to go through a process that identifies what’s going to work for the specific application and whether a standard system is available to support that application or if a custom solution is needed. Different systems have different requirements and conditions that have to be dealt with in addition to environmental concerns. Consider this example: Say your filtering at a remote site with some tough terrain; it would be difficult to bring a large heavy system that has to be carried a 100 Yards, so taking that into account will change the requirements and system needed to be able to safely and accurately accomplish the task by choosing the system best fit for how you will use it. In addition, there are certain informational aspects of providing application data such as ISO Standard cleanliness levels based on specific components or equipment (See Chart on page below.) where the Manufacturer suggested cleanliness requirements, especially for any warranty considerations, must be maintained. One additional application consideration is the space requirements and access of the area to which the filtration system will be applied; if you have limited space or the system is on a mezzanine this will also affect the system requirements. At this time also note any electrical or air limitations that may be encountered.
Question #2: What is the Oil Type/Viscosity?
Oil Type is a big factor in choosing and applying the proper filtration system because there is light, medium and heavy grades of oil or gear lubes and there is no such thing as a one system solution for all ISO Grades. With a risk of cross contamination, it is best practice to keep like grades of fluids together, and if you have more grades of oils then you do carts to maintain them, then its best to group them into categories of light, medium and heavy. Also, develop a good flushing procedure before going from one fluid to another of a differential ISO/viscosity grade. Additionally, the oil type will affect the systems pump flow requirement and fluid compatibility in relation to system seals, hoses and fittings.
Reference Oil Categories:
- Light Weight Oils: ISO 32, 46, 68
- Medium Weight Oils: ISO 150, 220
- Heavy Weight Oils: ISO 320, 680
Oil Types: *MSDS will do great in providing information pertaining to seal compatibility and the Manufacturer’s ISO Viscosity at two given temperatures 40°C and 100°C, this can be used to calculate pressure drop in a given system for sizing of hoses, pumps and Parallel or Series filter heads.
Question #3: Temperature/Environment of the Oil to be Filtered?
Temperature is one of the most unpredictable and causes the widest range of uncertainty in properly sizing and applying a filtration system. There are conditions or situations where the filtration system needs to operate in colder conditions where the temperature affects the viscosity of oils. Not so much a concern with lighter grades, but it becomes a big factor, especially with larger flow systems or medium to heavy grades of oils, to which the colder more viscous fluid makes it difficult to filter the oil properly and puts a great strain on the system’s ability to push the fluid through the pump, hoses and filters.
Question #4: How big is my sump or reservoir?
Some of the determining factors in choosing the pump flow size has a 3-part answer, questions # 2 & 3 from above and the size of the reservoir or sump to be filtered. Oil type and viscosity as mentioned above creates concerns around the viscosity of the fluid to be filtered. Temperature plays a part in fluctuating the oil viscosity which can effectively control the filtration systems ability to process the fluid. Normal or elevated temperatures may be within the capabilities of the filtration system but colder temps may throw them out. Finally, the reservoir or sump size also plays a big part in deciding which system can be applied successfully. It does no good to account for temperature and viscosity by a low flow pump especially when you consider larger 5000 gallon tanks. If you take the standard calculation of 7 passes of the reservoir size, divided by the pump flow in this example:
(5000 Gallons x 7 passes to circulate and completely clean a tank =35,000 Gallons / Pump Flow @ 2 GPM= 17,500 Minutes / 60 to convert to hours = 291.67 Hours to filter (12 Days), this would hardly make an impact on the cleanliness of the oil if it needs to be cleaned relatively quickly. If the ingression rate or particle and moisture generation is at a higher rate than what is being removed from the oil through the filtration system this effectively creates an obsolete system.
Question #5: ISO Cleanliness Class?
There is sometimes a little confusion when it comes to setting an ISO cleanliness level. We often get a comment like “I need a 3-micron filter” but it is a little more complex than just picking a micron level. Performance efficiencies of the filter and capacity of the element or DHC (Dirt Holding Capacity) are big factors to maintaining and achieving a set ISO code. There are some guiding rules to go by if no manufacturers recommendations are available. First, identify the most critical component most prone to failure due to contamination in your system and use a general specification or reference sheet based on applications to set a cleanliness standard. Your filter cart supplier should also be able to help you with setting the best ISO Cleanliness class for your system based on your specific conditions.
Suggested Acceptable Contamination Codes:
Source: Parker Hannifin Corp, Guid to Contamination Standards https://www.parker.com/literature/Hydraulic%20Filter/ConMon/Guide%20to%20Contamination%20Standards.pdf
Verification
Taking into account all the topics discussed above there is a final step in bringing everything together, and that is verifying that the system chosen is doing exactly as it is intended. To do this there needs to be a control method or process for verifying results, whether it be a fluid patch test, particle monitor or lab analysis. Filtration should never be a substitution for a great reliability program with checks and balances. A great reliability program includes a solution or process for handling new oil/bulk oil, an offline or online filtration system on a routine maintenance schedule and a verification or control process to enable you to follow each and every step all the way through to better reliability, up-time and of course a longer lasting system.
Summary of Questions to Answer
In summary, the FIVE questions to answer and three steps to an effective contamination control program are:
5 Questions:
- Application Information?
- Oil Type & Viscosity?
- Temperature of the Oil to be Filtered?
- Reservoir or Sump Size?
ISO Cleanliness Requirement?
3 Steps:
- Define Targets for Particle & Water Contamination and Oil Properties.
- Investigate Remedial Action as Necessary to Reach Targets.
- Monitor Contamination Levels Against Target Levels and Maintain Safe Levels.
Tip: Taking a look at time
Another consideration not mentioned in the questions above is time. This is typically gathered through the questions above, but is also a consideration to keep in mind for critical systems requiring immediate action. When filtering as a rule of thumb you want to size your pump, taking into considerations viscosity, temperature and time at least 10% of your reservoir or sump volume. (EX: 10% of a 5,000 Gallon reservoir = 500 Gallons/60 min (1HR) = 8.33 GPM) Of course Ingression rates, current contamination base samples and other factors and conditions will change the calculation, so always verify and confirm with the filtration system manufacturer to ensure the system your getting is capable of handling the system it will be used on.
Did I say simple guide? Nothing is ever simple you get out what you put in…..make sure to do your research and homework before putting your system at risk with a shot in the dark, take your knowledge and apply it well and watch the returns flow in.
FOR MORE INFORMATION
Y2K Filtration 3620 N. Lewis Ave. Sioux Falls, SD 57104 | 888-925-8882 |
sales@y2kfiltration.com Download PDF of Filtration System Sizing Guide